Modern agriculture depends on efficient NPK fertilizer production to meet global food demands. Specialized NPK machinery transforms raw materials into high-quality fertilizers through precise processes. This guide focuses on two essential components: NPK granulation equipment and NPK cooler, which work together to create uniform, stable fertilizer products.
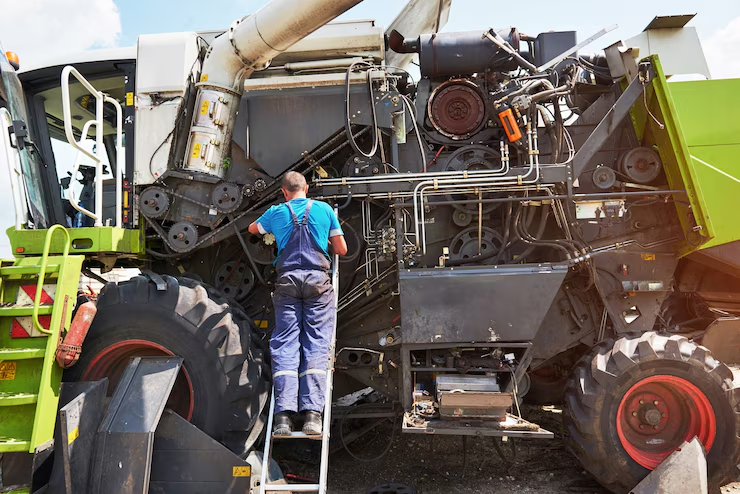
Understanding NPK Granulation Equipment
The Importance of Granulation in Fertilizer Production
Granulation converts powdered NPK mixtures into uniform granules that offer several advantages:
- Improved handling and application characteristics
- Reduced dust pollution during transport and spreading
- Controlled nutrient release patterns
- Enhanced storage stability
Types of NPK Granulation Systems
Rotary Drum Granulators
The most widely used granulation solution features:
- Continuous processing capability
- High throughput capacity (5-30 tons/hour)
- Excellent granule formation
- Adaptability to various formulations
Double Roller Extrusion Granulators
This dry granulation technology provides:
- No drying requirement (energy efficient)
- High granule density
- Precise size control
- Low maintenance operation
Disc Granulators
Known for their:
- Adjustable disc angle (35-55°)
- Excellent particle size uniformity
- Lower power consumption
- Compact footprint
The Critical Role of NPK Coolers
Why Cooling is Essential in NPK Production
Cooling systems perform vital functions:
- Stabilize granule structure after drying
- Reduce product temperature for safe storage
- Lower moisture content to prevent caking
- Prepare granules for coating processes
Advanced Cooling Technologies
Rotary Coolers
The industry standard offers:
- Counter-current air flow design
- Gentle product handling
- 20-30°C temperature reduction
- Integrated dust control
Fluidized Bed Coolers
Provide superior performance with:
- Rapid cooling (2-3 minute residence time)
- Excellent heat exchange efficiency
- Uniform product cooling
- Compact design
Vertical Vibrating Coolers
Space-saving alternatives featuring:
- Multi-stage cooling process
- Low energy consumption
- Minimal footprint
- Easy maintenance access
Selecting the Right NPK Machinery
Granulation Equipment Selection Factors
Key considerations include:
- Production capacity requirements
- Raw material characteristics
- Energy efficiency needs
- Available facility space
- Maintenance requirements
Cooler Selection Criteria
Important specifications to evaluate:
- Cooling capacity (tons/hour)
- Temperature reduction capability
- Airflow volume and pattern
- Dust control efficiency
- Energy consumption
Optimizing NPK Production Performance
Granulation Process Improvements
Advanced techniques to enhance quality:
- Steam conditioning for better plasticity
- Binder optimization for strength
- Particle size distribution control
- Real-time process monitoring
Cooling System Enhancements
Modern cooling strategies include:
- Heat recovery systems
- Humidity-controlled air supply
- Automated temperature adjustment
- Predictive maintenance programs
Maintenance Best Practices
Granulation Equipment Care
Essential maintenance routines:
- Daily inspection of critical components
- Regular lubrication schedules
- Wear part replacement protocols
- Alignment verification
Cooler Maintenance Guidelines
Critical upkeep procedures:
- Air distribution system checks
- Screen deck inspections
- Bearing maintenance
- Drive system evaluation
Emerging Technologies in NPK Machinery
Future developments include:
- AI-powered process optimization
- IoT-enabled equipment monitoring
- Sustainable energy solutions
- Modular plant designs
- Advanced material coatings
Conclusion
Investing in quality NPK granulation equipment and coolers delivers significant benefits:
- Consistent product quality meeting market standards
- Optimized production efficiency
- Reduced energy consumption
- Extended equipment lifespan
- Improved operational safety
For operations considering equipment upgrades, consulting with experienced NPK machinery providers ensures selecting solutions tailored to specific production needs. The right combination of granulation and cooling technology can transform fertilizer production operations.